For a boiler to function efficiently, the boiler feed water that runs it must be of the best quality possible. Impurities can cause problems like operational issues, inefficient flow, and equipment damage. Many of these issues can be mitigated or prevented with an appropriate water filtration system.
Here are some common problems associated with boiler-feed water and the best ways to mitigate them.
Scale Formation
If the system has trouble keeping steady pressure and temperature, there could be scale deposits in the system that are partially blocking the flow. Scale forms when there are high levels of calcium, magnesium, lime, and other forms of hard water in the system. This buildup reduces heat transfer efficiency, leading to higher fuel costs and potential equipment damage.
Water softening is the most common way to treat and prevent scale formation. Depending on the level of buildup, you may also need to look into solutions like acid cleaning, reverse osmosis, and parts replacements.
Corrosion
Signs of corrosion usually include rust, pitting, or discoloration on the boiler components or pipework. It could also be the source of discolored liquid, changes in pH levels, and unexplained frequent leaks and parts failures
Corrosion can occur if the seals, rings, or inner linings are made from materials that chemically react to the impurities in the system. This corrosion physically weakens and breaks down the equipment. This leads to equipment damage and potential system failures.
Once corrosion occurs, the part is irreversibly damaged. The first step to avoiding corrosion is making sure all parts, hoses, seals, and other components of the boiler feed system are made to withstand any potential interactions with the fluid, hard water, oxygen, and various impurities.
A few other treatments and preventions include:
- Deaeration. Mechanical deaerators heat the feed water and remove dissolved gases.
- pH Control. Maintaining a slightly alkaline pH level by adding pH-adjusting chemicals.
- Corrosion Inhibitors. These chemicals form a protective film on the metal surfaces to prevent contact with corrosive elements in the water.
Contamination and Carryover
Cloudy or discolored steam, or the presence of impurities in downstream equipment, can indicate carryover issues. Carryover happens when impurities in the feed water get carried into the steam. This affects steam quality and can damage downstream equipment.
Opt for a boiler with design features that minimize carryover. Some examples include a steam separator or a large steam drum. Using filters or ion exchange systems in the feed water lines can also remove impurities before they enter the boiler. Our experts can help you find the best solutions for your equipment.
Best Practices for Optimal Boiler Feed Water Treatment
Keeping these common issues in check involves proactive testing and monitoring. Here are a few ways to keep your boiler feed working its best.
- Regularly test the feed water for impurities. This will help you detect issues early before costly repairs are necessary.
- Invest in high-quality treatment systems that effectively filter and treat feed water. Our specialists can help you narrow down some of the best choices for your equipment.
- Ensure staff are equipped to manage the boil feed system effectively.
- Regular maintenance, repairs, and replacements can help you detect issues and minimize their overall costs to your business.
- Make sure the system has the filters, softeners, and supporting equipment it needs. Check with your industrial filtration experts for the best ways to support your equipment.
Prevention is always better than a cure, especially when it comes to boiler maintenance. Ensuring the quality of boiler feed water is crucial for the efficient operation of boilers and the longevity of the equipment.
Sparkling Clear’s Experts Can Help You Troubleshoot Your Boiler Feed Filtration Issues
We provide the most comprehensive, customer-friendly, customized commercial filtration services to help you accomplish more in less time. Don’t let issues build up into costly repairs. Contact us today to find out the best treatment and prevention solutions for your business!
\
Share this Post!
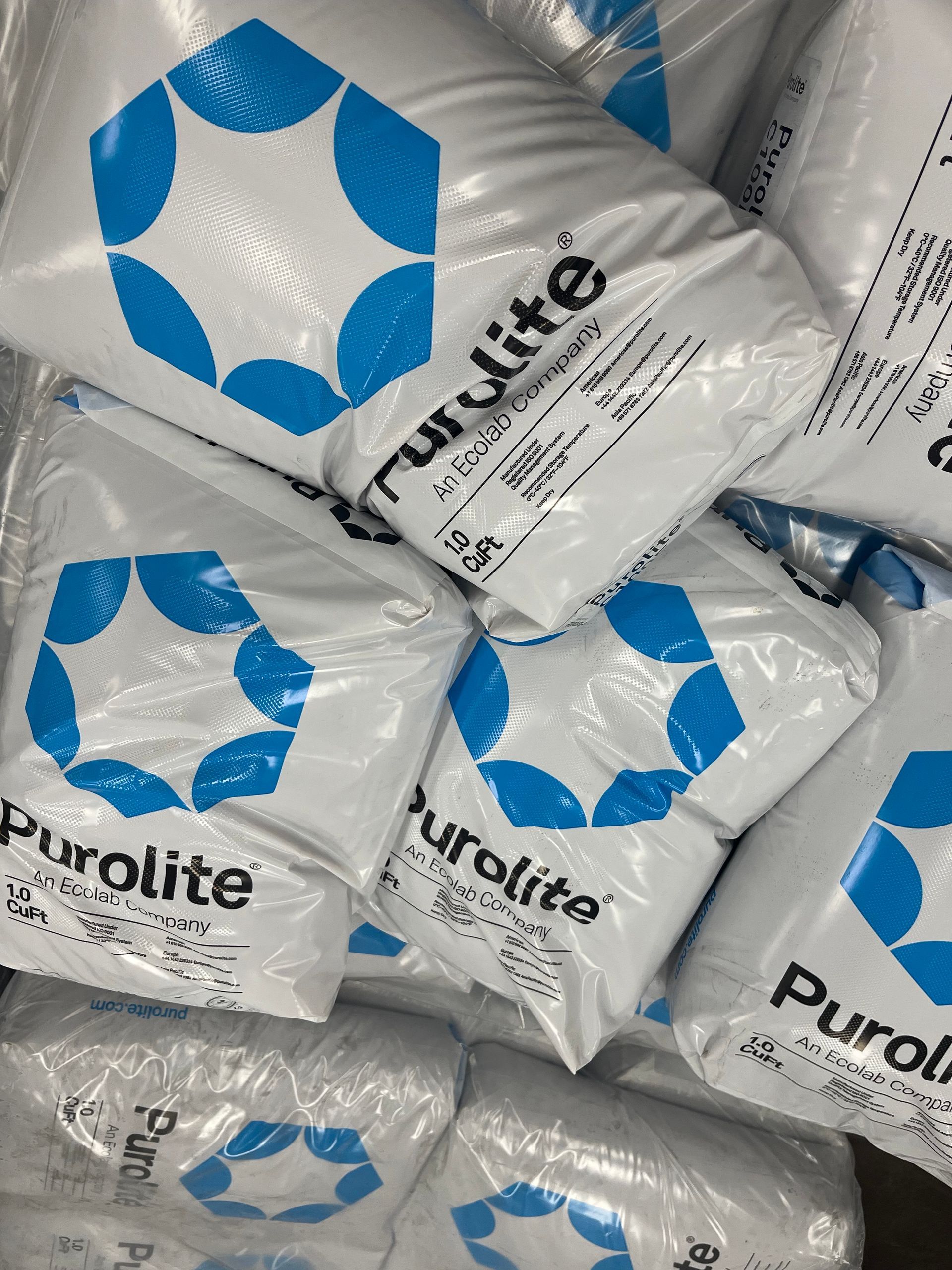