Why Use Membranes?
July 16, 2024
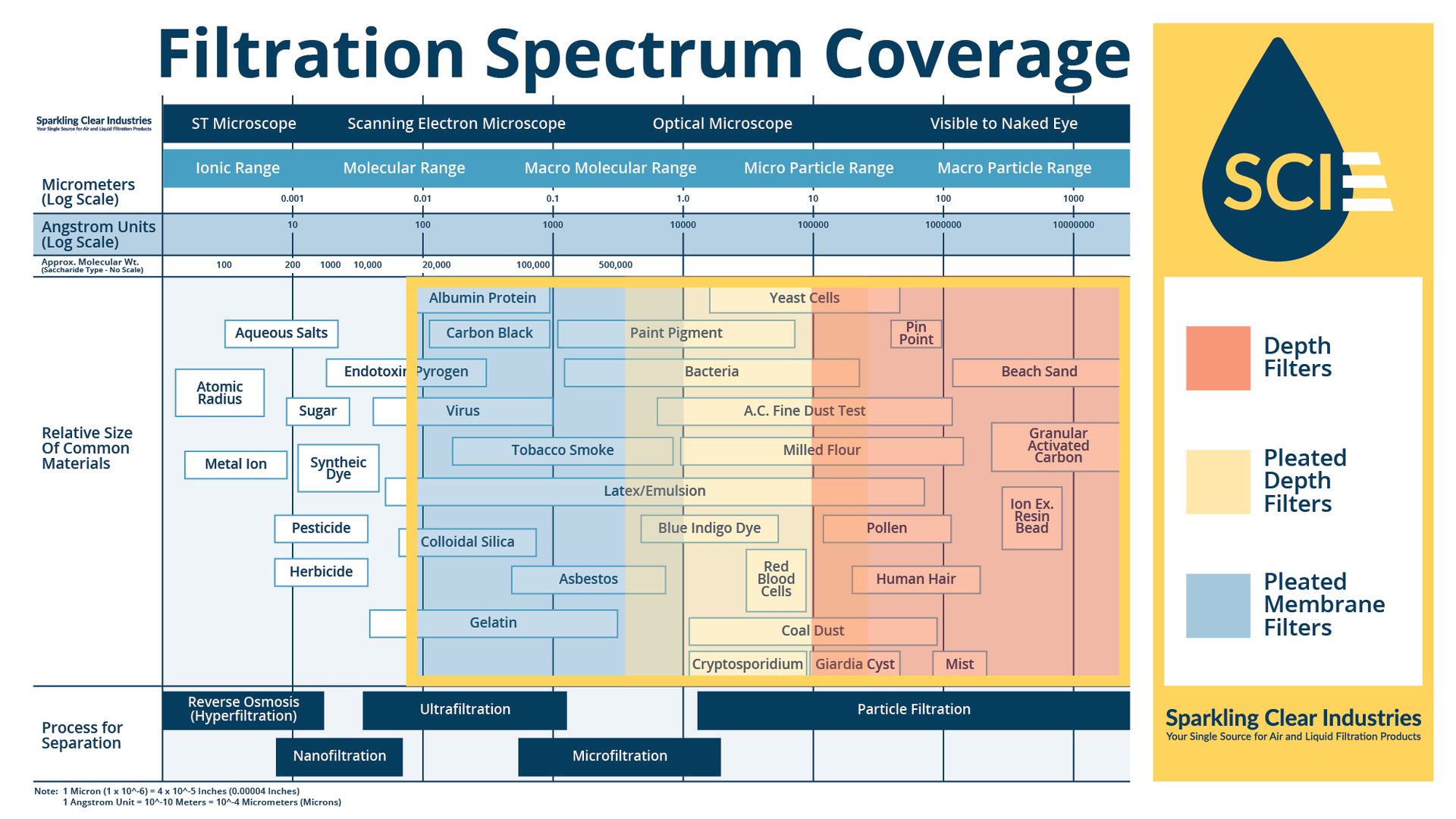
At Sparkling Clear, we understand the importance of using membrane cartridges for filtration. The pore structure of our membrane cartridges ensures extremely high retention efficiency and consistent effluent quality. This capability to capture and retain very small particulates and organisms instills a high degree of confidence that your product will be clean and safe for use.
The consistent pore structure of our membranes also allows for straightforward testing, helping both manufacturers and users to understand and communicate the expected performance of the cartridge in various applications. This is why membrane filters are typically employed in scenarios where the removal of submicronic contaminants is crucial.
It is important to note that membrane filters are generally used in the final stages of a filtration process. To ensure the longevity and efficiency of the membrane cartridge, it is essential to protect it with prefilters. This protection prevents premature fouling and maximizes the economic value of the system.
Applications that Usually Require Membranes:
- Submicronic particulate removal
- Removal of microorganisms (bacteria, viruses, etc.)
- Applications requiring sterility (liquid or gas)
- Endotoxin removal
- Haze removal (typically caused by high concentrations of particles at or below 0.45 microns)
Choose Sparkling Clear for your membrane filtration needs to ensure the highest quality and safety of your products.