Sparkling Clear Industries, Inc. (SCI), with offices in Houston and Clute, has been awarded the distribution rights in Central/South Texas for the Fluid Engineering (FE) line of strainers as well as the TM Filtration line of Gas Coalescing Filters.
FE strainers, which are used in many liquid applications to filter out coarse particles (>50 micron), can be supplied in many different configurations from a simple inline cone strainer to a custom engineered automatic self-cleaning strainer fabricated from exotic metals such as Hastelloy C276 or 2507 Super Duplex Stainless Steel (Zeron 100). The Fluid Engineering automatic self-cleaning strainers have the most effective and efficient cleaning cycle of ANY strainer manufacturer in the industry. With the exception of some of their cast components, all of their strainers are manufactured to their customer’s specifications in the United States. This includes not only the strainers but the skids, control panels and any special requirements such as rubber lining or specialty coatings.
TM Filtration’s Gas Flow Membrane (GFM) technology gives natural gas producers an improved way to block unwanted carryover associated with wetter unconventional gas sources such as shale and biogas. In a traditional gas coalescing filter, extracted liquids and contaminants (collectively known as carryover) can be drawn back into the gas stream through a process known as re-entrainment. This is due to the fact that in traditional coalescing units, gas enters the inside of the filter element and flows to the outside. The result is that when the water drops out of the element it has to travel toward the discharge against the same gas stream that took it into the inside of the cartridge in the first place.
The TM Filtration GFM Technology addresses and effectively eliminates this issue by utilizing a reverse flow design through the pleated GFM filter element. Instead of trying to filter the gas on the inside of the filter cartridge, the TM design passes the gas from the outside of the element to the inside. This is, in fact, more efficient and is the way that most all other forms of cartridge filtration operate.
The process begins as the gas enters the vessel and is directed into a tangential circular flow pattern by radial impingement plates. The centrifugal force separates and removes large particles and slugs of liquid. In the second stage, gas flows upward through either a mechanical mesh or vane scrubber to remove medium-sized particles. The third and final stage of filtration occurs in the GFM filter element. Due to the pleated construction the element has up to 20 times the filtration area of traditional filter elements. The water stays on the outside of the element and only dry gas passes through on the way to the discharge from the filter.
The net result of this advanced design is cleaner gas streams at reduced operational cost.
Call our Houston office at 713-956-8900 or our Clute office at 979-265-6555 to schedule a technical presentation of the unique features and benefits of both of these product lines. You can also visit us on our website at www.sparklingclear.com.
The post Sparkling Clear Industries Introduces New Product Lines appeared first on Sparkling Clear.
Share this Post!
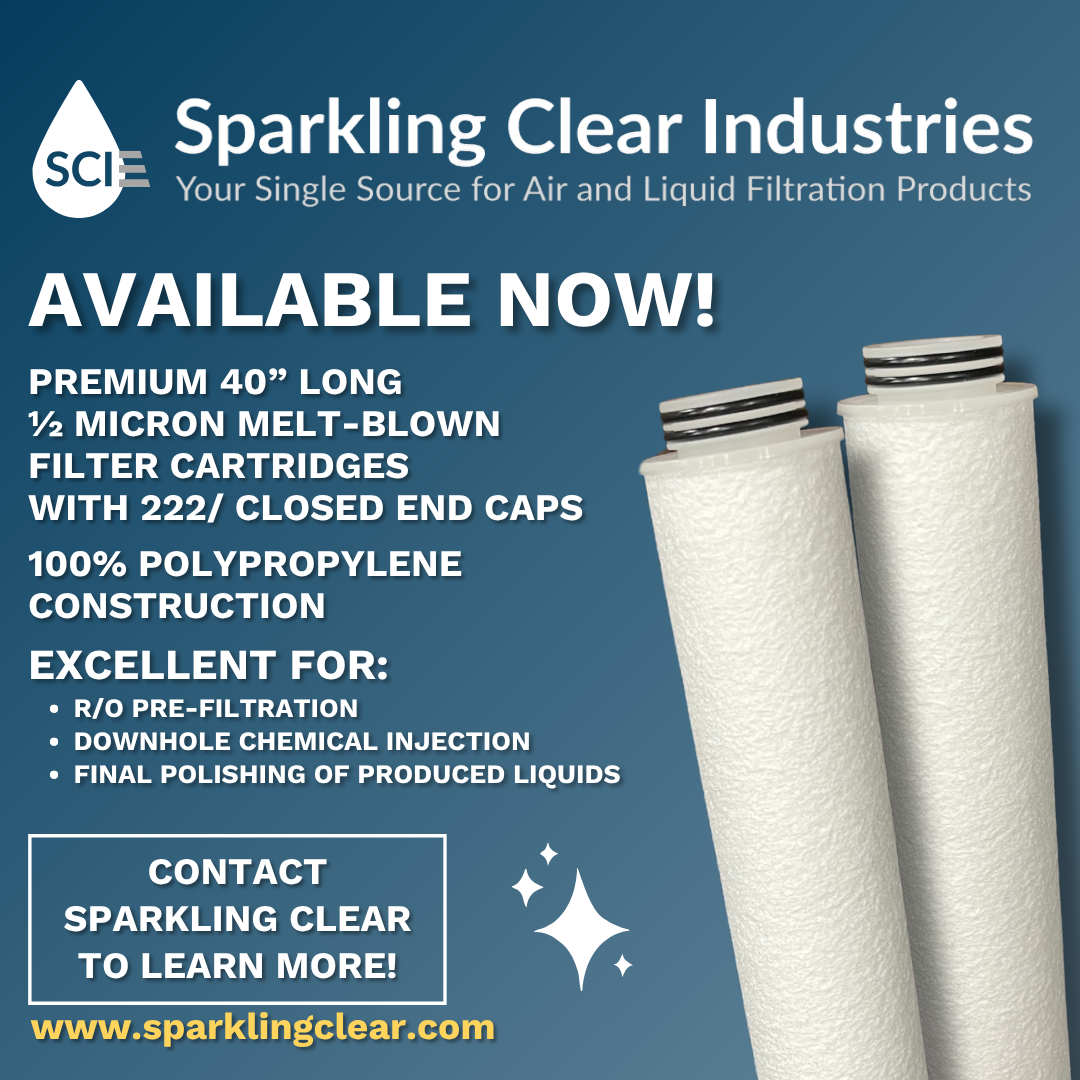
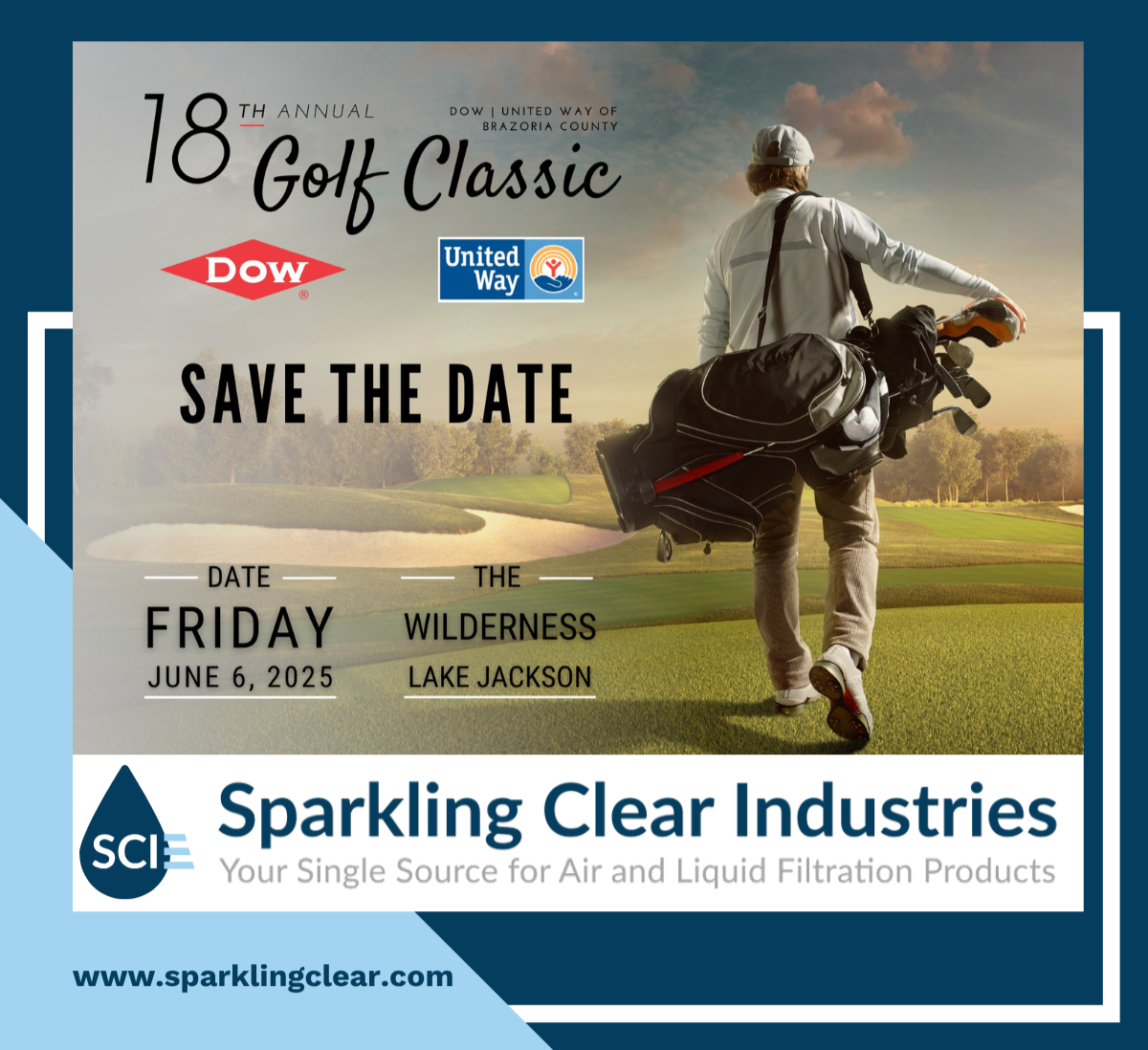